Lock Bolt & Collar Description
Lock bolts and collars are mechanical fasteners used in various applications to secure components together. Here’s a brief overview of each:
Lock Bolts
Definition
Lock bolts are a type of fastener that provides a secure, tamper-resistant connection. They often consist of a bolt, a collar, and a locking mechanism.
Applications
Commonly used in construction, automotive, and aerospace industries where high strength and vibration resistance are required.
Advantages
High strength and reliability.
Quick installation with specialized tools.
Reduced risk of loosening under load or vibration.
Collars
Definition
Collars are circular devices that can be used to secure or position components along a shaft or rod. They can come in various designs, such as set screw collars or clamp collars.
Applications
Used in machinery, automotive, and robotics to hold parts in place, prevent axial movement, or act as stops.
Advantages
Easy to install and adjust.
Versatile for different applications.
Helps maintain alignment and prevent wear.
Manufacturing Processing of Lock Bolts and Collars
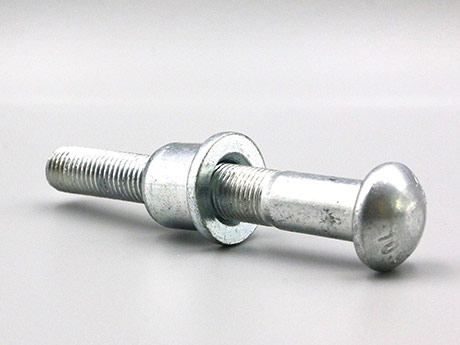
Material Selection
Raw Materials: High-strength steel or other alloys are commonly used due to their durability and load-bearing capacity.
Coatings: Corrosion-resistant coatings may be applied depending on the intended application.
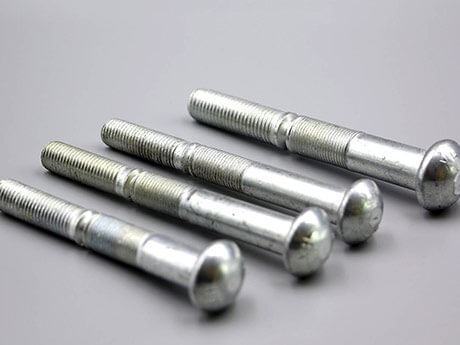
Forging or Machining
Forging: The raw material is heated and shaped into the basic form of the bolt, which enhances its strength.
Machining: Precision machining is performed to create the threads and define the dimensions of the bolt and collar.
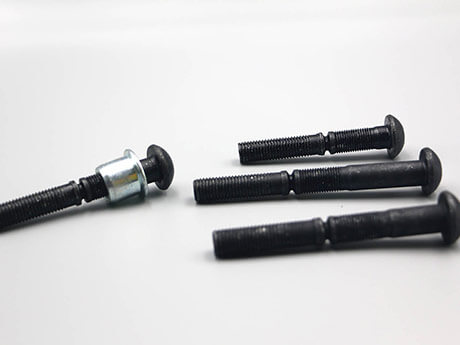
Heat Treatment
Hardening: The bolts may undergo heat treatment processes like quenching and tempering to increase hardness and strength.
Annealing: Sometimes used to relieve stresses and improve machinability.
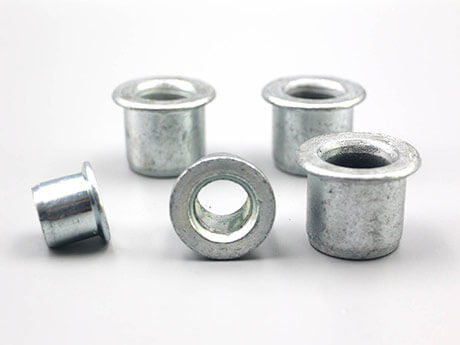
Surface Finishing
Cleaning: The bolts are cleaned to remove any debris or oil.
Coating: Protective coatings, such as zinc plating or other finishes, are applied to prevent corrosion.
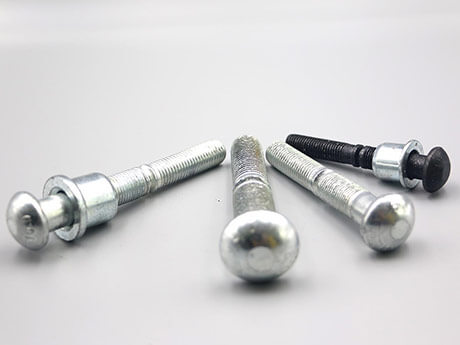
Assembly of Lock Mechanism
Collar Attachment: The collar is attached to the bolt, ensuring the design allows for secure locking.
Locking Mechanism: Depending on the design, the locking mechanism may be integrated during this stage.
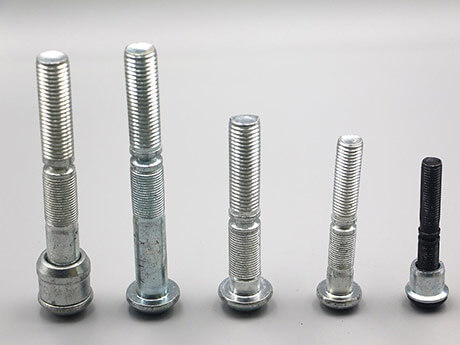
Quality Control
Inspection: Each batch undergoes rigorous testing for dimensional accuracy, strength, and surface quality.
Testing: Mechanical tests may include tensile testing, hardness testing, and fatigue testing to ensure reliability.
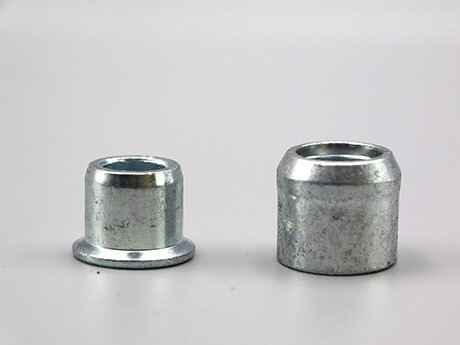
Packaging and Shipping
Packaging: Finished lock bolts are packaged to prevent damage during transport.
Distribution: They are shipped to distributors or directly to customers for use in various applications.
Common Steel Code
Grades Comparison
CHINA/GB | ISO | ГΟСТ | ASTM | JIS | DIN |
45 | C45E4 | 45 | 1045 | S45C | CK45 |
20MnTiB | |||||
ML08Al | 1008 |
Most used Materials for Lock bolts and Collars
- Carbon Steel
Excellent strength and hardness.
Commonly used in general applications. - Alloy Steel
Enhanced strength and toughness.
Suitable for high-stress applications. - Stainless Steel
Corrosion-resistant.
Ideal for marine and chemical environments. - Common grades: 304, 316.
Common Heat Treatment Process
Heat treatment is a crucial process in the production of lock bolts and collars, enhancing their mechanical properties to meet specific application requirements. Here’s an overview of the heat treatment processes commonly applied:
01
Hardening
Purpose
Increases hardness and strength by transforming the microstructure of the steel into martensite.
Process
The bolts and collars are heated to a high temperature (typically above the critical temperature) and then rapidly cooled (quenched) using oil or water.
02
Tempering
Purpose
Reduces brittleness introduced during hardening, improving toughness while retaining much of the hardness.
Process
After hardening, the components are reheated to a lower temperature (typically between 150°C to 650°C) for a specific duration, then cooled.
03
Normalizing
Purpose
Produces a uniform microstructure, enhancing strength and toughness while improving machinability.
Process
Similar to annealing, but the components are air-cooled after heating.
04
Annealing
Purpose
Relieves internal stresses, improves machinability, and refines the microstructure for better ductility.
Process
The components are heated to a specific temperature and then allowed to cool slowly in a furnace.
Diameter of Lock Bolts and Collars
Nominal Diameter | Actual Diameter | Nominal Riveting Thickness | Actual Riveting Thickness | Huck Model | Avdel Model | ||
Min | Max | Min | Max | ||||
5 (3/16″) | 4.85 | 4.95 | 3 | 1.6 | 4.8 | C6LB-R6-2G | 02621-70602 |
5 | 3.2 | 6.4 | C6LB-R6-3G | 02621-70603 | |||
6 | 4.8 | 7.9 | C6LB-R6-4G | 02621-70604 | |||
8 | 6.4 | 9.5 | C6LB-R6-5G | 02621-70605 | |||
10 | 7.9 | 11.1 | C6LB-R6-6G | 02621-70606 | |||
11 | 9.5 | 12.7 | C6LB-R6-7G | 02621-70607 | |||
13 | 11.1 | 14.3 | C6LB-R6-8G | 02621-70608 | |||
14 | 12.7 | 15.9 | C6LB-R6-9G | 02621-70609 | |||
16 | 14.3 | 17.5 | C6LB-R6-10G | 02621-70610 | |||
17 | 15.9 | 19.1 | C6LB-R6-11G | 02621-70611 | |||
19 | 17.5 | 20.7 | C6LB-R6-12G | 02621-70612 | |||
21 | 19.1 | 22.2 | C6LB-R6-13G | 02621-70613 | |||
22 | 20.7 | 23.8 | C6LB-R6-14G | 02621-70614 | |||
24 | 22.2 | 25.4 | C6LB-R6-15G | 02621-70615 | |||
25 | 23.8 | 27 | C6LB-R6-16G | 02621-70616 | |||
27 | 25.4 | 28.6 | C6LB-R6-17G | 02621-70617 | |||
28 | 27 | 30.2 | C6LB-R6-18G | 02621-70618 | |||
30 | 28.6 | 31.8 | C6LB-R6-19G | 02621-70619 | |||
32 | 30.2 | 33.4 | C6LB-R6-20G | 02621-70620 | |||
6 (1/4”) | 6.45 | 6.58 | 3 | 1.6 | 4.8 | C6LB-R8-2G | 02621-70802 |
5 | 3.2 | 6.4 | C6LB-R8-3G | 02621-70803 | |||
6 | 4.8 | 7.9 | C6LB-R8-4G | 02621-70804 | |||
8 | 6.4 | 9.5 | C6LB-R8-5G | 02621-70805 | |||
10 | 7.9 | 11.1 | C6LB-R8-6G | 02621-70806 | |||
11 | 9.5 | 12.7 | C6LB-R8-7G | 02621-70807 | |||
13 | 11.1 | 14.3 | C6LB-R8-8G | 02621-70808 | |||
14 | 12.7 | 15.9 | C6LB-R8-9G | 02621-70809 | |||
16 | 14.3 | 17.5 | C6LB-R8-10G | 02621-70810 | |||
17 | 15.9 | 19.1 | C6LB-R8-11G | 02621-70811 | |||
19 | 17.5 | 20.7 | C6LB-R8-12G | 02621-70812 | |||
21 | 19.1 | 22.2 | C6LB-R8-13G | 02621-70813 | |||
22 | 20.7 | 23.8 | C6LB-R8-14G | 02621-70814 | |||
24 | 22.2 | 25.4 | C6LB-R8-15G | 02621-70815 | |||
25 | 23.8 | 27 | C6LB-R8-16G | 02621-70816 | |||
27 | 25.4 | 28.6 | C6LB-R8-17G | 02621-70817 | |||
28 | 27 | 30.2 | C6LB-R8-18G | 02621-70818 | |||
30 | 28.6 | 31.8 | C6LB-R8-19G | 02621-70819 | |||
32 | 30.2 | 33.4 | C6LB-R8-20G | 02621-70820 | |||
8 (5/16”) | 8.05 | 8.18 | 6 | 3.2 | 9.5 | C6LB-R10-4G | 02621-71004 |
10 | 6.4 | 12.7 | C6LB-R10-6G | 02621-71006 | |||
13 | 9.5 | 15.9 | C6LB-R10-8G | 02621-71008 | |||
16 | 12.7 | 19.1 | 8.05~8.18 | 02621-71010 | |||
19 | 15.9 | 22.2 | C6LB-R10-12G | 02621-71012 | |||
22 | 19.1 | 25.4 | C6LB-R10-14G | 02621-71014 | |||
25 | 22.2 | 28.6 | C6LB-R10-16G | 02621-71016 | |||
28 | 25.4 | 31.8 | C6LB-R10-18G | 02621-71018 | |||
32 | 28.6 | 34.9 | C6LB-R10-20G | 02621-71020 | |||
10 (3/8”) | 9.65 | 9.78 | 6 | 3.2 | 9.5 | C6LB-R12-4G | 02621-71204 |
10 | 6.4 | 12.7 | C6LB-R12-6G | 02621-71206 | |||
13 | 9.5 | 15.9 | C6LB-R12-8G | 02621-71208 | |||
16 | 12.7 | 19.1 | C6LB-R12-10G | 02621-71210 | |||
19 | 15.9 | 22.2 | C6LB-R12-12G | 02621-71212 | |||
22 | 19.1 | 25.4 | C6LB-R12-14G | 02621-71214 | |||
25 | 22.2 | 28.6 | C6LB-R12-16G | 02621-71216 | |||
28 | 25.4 | 31.8 | C6LB-R12-18G | 02621-71218 | |||
32 | 28.6 | 34.9 | C6LB-R12-20G | 02621-71220 | |||
12 (1/2”) | 12.5 | 13.1 | 6 | 6.35 | 12.7 | C50LR-BR16-4 | 02861-01604 |
12 | 12.7 | 19.1 | C50LR-BR16-8 | 02861-01608 | |||
18 | 19.1 | 25.4 | C50LR-BR16-12 | 02861-01612 | |||
24 | 25.4 | 31.8 | C50LR-BR16-16 | 02861-01616 | |||
31 | 31.8 | 38.1 | C50LR-BR16-20 | 02861-01620 | |||
37 | 38.1 | 44.5 | C50LR-BR16-24 | 02861-01624 | |||
44 | 44.5 | 50.8 | C50LR-BR16-28 | 02861-01628 | |||
50 | 50.8 | 57.2 | C50LR-BR16-32 | 02861-01632 | |||
57 | 57.2 | 63.5 | C50LR-BR16-36 | 02861-01636 | |||
63 | 63.5 | 69.9 | C50LR-BR16-40 | 02861-01640 | |||
70 | 69.8 | 76.2 | C50LR-BR16-44 | 02861-01644 | |||
77 | 76.2 | 82.6 | C50LR-BR16-48 | 02861-01648 | |||
83 | 82.6 | 88.9 | C50LR-BR16-52 | 02861-01652 | |||
89 | 88.9 | 95.3 | C50LR-BR16-56 | 02861-01656 | |||
95 | 95.3 | 101.6 | C50LR-BR16-60 | 02861-01660 | |||
16 (5/8”) | 15.7 | 16.3 | 6 | 6.35 | 12.7 | C50LR-BR20-4 | 02861-02004 |
12 | 12.7 | 19.1 | C50LR-BR20-8 | 02861-02008 | |||
18 | 19.1 | 25.4 | C50LR-BR20-12 | 02861-02012 | |||
24 | 25.4 | 31.8 | C50LR-BR20-16 | 02861-02016 | |||
31 | 31.8 | 38.1 | C50LR-BR20-20 | 02861-02020 | |||
37 | 38.1 | 44.5 | C50LR-BR20-24 | 02861-02024 | |||
44 | 44.5 | 50.8 | C50LR-BR20-28 | 02861-02028 | |||
50 | 50.8 | 57.2 | C50LR-BR20-32 | 02861-02032 | |||
57 | 57.2 | 63.5 | C50LR-BR20-36 | 02861-02036 | |||
63 | 63.5 | 69.9 | C50LR-BR20-40 | 02861-02040 | |||
70 | 69.8 | 76.2 | C50LR-BR20-44 | 02861-02044 | |||
77 | 76.2 | 82.6 | C50LR-BR20-48 | 02861-02048 | |||
83 | 82.6 | 88.9 | C50LR-BR20-52 | 02861-02052 | |||
89 | 88.9 | 95.3 | C50LR-BR20-56 | 02861-02056 | |||
95 | 95.3 | 101.6 | C50LR-BR20-60 | 02861-02060 | |||
20 (3/4”) | 18.8 | 19.5 | 6 | 6.35 | 12.7 | C50LR-BR24-4 | 02861-02404 |
12 | 12.7 | 19.1 | C50LR-BR24-8 | 02861-02408 | |||
18 | 19.1 | 25.4 | C50LR-BR24-12 | 02861-02412 | |||
24 | 25.4 | 31.8 | C50LR-BR24-16 | 02861-02416 | |||
31 | 31.8 | 38.1 | C50LR-BR24-20 | 02861-02420 | |||
37 | 38.1 | 44.5 | C50LR-BR24-24 | 02861-02424 | |||
44 | 44.5 | 50.8 | C50LR-BR24-28 | 02861-02428 | |||
50 | 50.8 | 57.2 | C50LR-BR24-32 | 02861-02432 | |||
57 | 57.2 | 63.5 | C50LR-BR24-36 | 02861-02436 | |||
63 | 63.5 | 69.9 | C50LR-BR24-40 | 02861-02440 | |||
70 | 69.8 | 76.2 | C50LR-BR24-44 | 02861-02444 | |||
77 | 76.2 | 82.6 | C50LR-BR24-48 | 02861-02448 | |||
83 | 82.6 | 88.9 | C50LR-BR24-52 | 02861-02452 | |||
89 | 88.9 | 95.3 | C50LR-BR24-56 | 02861-02456 | |||
95 | 95.3 | 101.6 | C50LR-BR24-60 | 02861-02460 | |||
22 (7/8”) | 22.0 | 22.7 | 12 | 12.7 | 19.1 | C50LR-BR28-8 | 02861-02808 |
18 | 19.1 | 25.4 | C50LR-BR28-12 | 02861-02812 | |||
24 | 25.4 | 31.8 | C50LR-BR28-16 | 02861-02816 | |||
31 | 31.8 | 38.1 | C50LR-BR28-20 | 02861-02820 | |||
37 | 38.1 | 44.5 | C50LR-BR28-24 | 02861-02824 | |||
44 | 44.5 | 50.8 | C50LR-BR28-28 | 02861-02828 | |||
50 | 50.8 | 57.2 | C50LR-BR28-32 | 02861-02832 | |||
57 | 57.2 | 63.5 | C50LR-BR28-36 | 02861-02836 | |||
63 | 63.5 | 69.9 | C50LR-BR28-40 | 02861-02840 | |||
70 | 69.8 | 76.2 | C50LR-BR28-44 | 02861-02844 | |||
77 | 76.2 | 82.6 | C50LR-BR28-48 | 02861-02848 | |||
83 | 82.6 | 88.9 | C50LR-BR28-52 | 02861-02852 | |||
89 | 88.9 | 95.3 | C50LR-BR28-56 | 02861-02856 | |||
95 | 95.3 | 101.6 | C50LR-BR28-60 | 02861-02860 | |||
25 (1”) | 25.1 | 26 | 12 | 12.7 | 19.1 | C50LR-BR32-8 | 02861-03208 |
18 | 19.1 | 25.4 | C50LR-BR32-12 | 02861-03212 | |||
24 | 25.4 | 31.8 | C50LR-BR32-16 | 02861-03216 | |||
31 | 31.8 | 38.1 | C50LR-BR32-20 | 02861-03220 | |||
37 | 38.1 | 44.5 | C50LR-BR32-24 | 02861-03224 | |||
44 | 44.5 | 50.8 | C50LR-BR32-28 | 02861-03228 | |||
50 | 50.8 | 57.2 | C50LR-BR32-32 | 02861-03232 | |||
57 | 57.2 | 63.5 | C50LR-BR32-36 | 02861-03236 | |||
63 | 63.5 | 69.9 | C50LR-BR32-40 | 02861-03240 | |||
70 | 69.8 | 76.2 | C50LR-BR32-44 | 02861-03244 | |||
77 | 76.2 | 82.6 | C50LR-BR32-48 | 02861-03248 | |||
83 | 82.6 | 88.9 | C50LR-BR32-52 | 02861-03252 | |||
89 | 88.9 | 95.3 | C50LR-BR32-56 | 02861-03256 | |||
95 | 95.3 | 101.6 | C50LR-BR32-60 | 02861-03260 |
Collar Type | Nominal Diameter | Huck Model | Avdel Model |
LMTP | 5 | 2LC-R6G | 02662-70600 |
6 | 2LC-R8G | 02662-70800 | |
8 | 2LC-R10G | 02662-71000 | |
10 | 2LC-R12G | 02662-71200 | |
12 | LC-2R16G | 02662-01600 | |
16 | LC-2R20G | 02662-02000 | |
20 | LC-2R24G | 02662-02400 | |
22 | LC-2R28G | 02662-02800 | |
25 | LC-2R32G | 02662-03200 | |
LMTF | 5 | 3LC-R6G | 02615-70600 |
6 | 3LC-R8G | 02615-70800 | |
8 | 3LC-R10G | 02615-71000 | |
10 | 3LC-R12G | 02615-71200 | |
12 | 3LC-R16G | 02615-01600 | |
16 | 3LC-R20G | 02615-02000 | |
20 | 3LC-R24G | 02615-02400 | |
22 | 3LC-R28G | 02615-02800 | |
25 | 3LC-R32G | 02615-03200 | |
LMTJ | 5 | 8LC-R6G | 02682-70600 |
6 | 8LC-R8G | 02682-70800 | |
8 | 8LC-R10G | 02682-71000 | |
10 | 8LC-R12G | 02682-71200 | |
12 | 8LC-R16G | – | |
16 | 8LC-R20G | – | |
20 | 8LC-R24G | – | |
22 | 8LC-R28G | – | |
25 | 8LC-R32G | – |