Gear Shaft Description
Gear shaft is an important mechanical transmission element, widely used in all kinds of mechanical equipment.
It consists of gears and shafts, and realizes power transmission and speed change function through the combination of gears and shafts.
Gear shafts have various forms and types, We mainly produce two types of gear shafts: transmission gear shafts and spline gear shafts.
Transmission gear shaft is an important mechanical transmission element, which realizes power transmission and variable speed function through the combination of gear and shaft.
Spline gear shaft is an important mechanical transmission component, It can efficiently transmit mechanical torque and realize precise rotary and linear motion through special tooth design.
Through the direct combination of gears and shafts, gear shafts can efficiently transmit power and motion with high transmission efficiency. The compact design of gear shafts occupies little space and is suitable for a wide range of mechanical devices, especially in occasions where space is limited.
Gear shafts are able to withstand large torque and axial force, suitable for high load transmission system. By adopting high quality materials and precision processing, gear shafts produce low noise during operation, which is conducive to improving the working environment.
Manufacturing Method of Gear Shaft
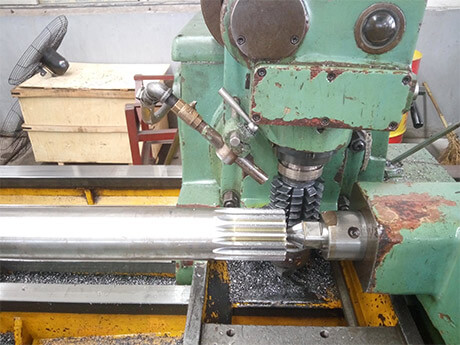
Gear Hobbing/Spline Hobbing
Description: A gear cutting process that uses a hob (a specialized cutting tool) to shape the gear teeth.
Advantages: Suitable for high-volume production; efficient and cost-effective for manufacturing gears with complex tooth profiles.
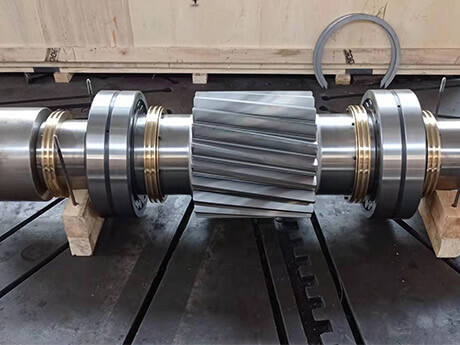
Gear Shaping/Spline Shaping
Description: Involves a shaping machine that uses a reciprocating cutter to remove material and form the gear teeth.
Advantages: Can produce gears of various sizes and tooth profiles; effective for low-volume runs and custom gears.
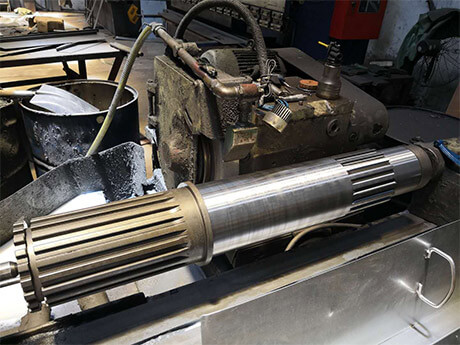
Gear Milling/Spline Milling
Description: Uses a milling machine to cut the gear teeth. This method is often used for smaller gears or specialized shapes.
Advantages: Versatility in producing different gear types and sizes; can be used for both prototype and production runs.
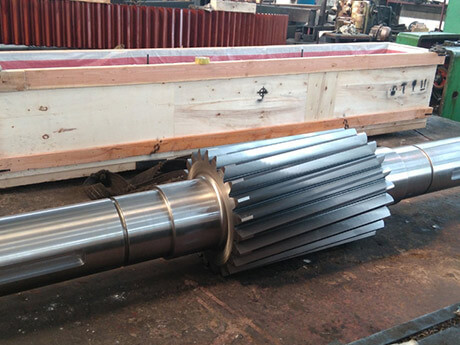
Gear Grinding/Spline Grinding
Description: Involves using a grinding wheel to refine the tooth profile and achieve precise dimensions and surface finishes.
Advantages: Provides high accuracy and smooth surface finishes; often used as a secondary process after hobbing or shaping.
Common Steel Code
Grades Comparison
CHINA/GB | ISO | ROCT | ASTM | JIS | DIN |
45 | C45E4 | 45 | 1045 | S45C | CK45 |
40Cr | 41Cr4 | 40X | 5140 | SCr440 | 41Cr4 |
20CrMo | 18CrMo4 | 20ХМ | 4118 | SCM22 | 25CrMo4 |
42CrMo | 42CrMo4 | 38XM | 4140 | SCM440 | 42CrMo4 |
20CrMnTi | 18XГT | SMK22 | |||
20Cr2Ni4 | 20X2H4A | ||||
20CrNiMo | 20CrNiMo2 | 20XHM | 8720 | SNCM220 | 21NiCrMo2 |
40CrNiMoA | 40XH2MA/ 40XHMA | 4340 | SNCM439 | ||
20CrNi2Mo | 20NiCrMo7 | 20XH2MA | 4320 | SNCM420 | |
17CrNiMo6 | |||||
18CrNiMo7 |
Common Heat Treatment Process
Heat treatment is a controlled process used to alter the physical and sometimes chemical properties of materials, particularly metals. It can enhance properties such as hardness, strength, toughness, and ductility. Here are some common heat treatment processes:
01
Annealing
Purpose
To soften the material, improve ductility, and relieve internal stresses.
Process
Heating the metal to a specific temperature and then cooling it slowly, usually in air or in a furnace.
02
Quenching
Purpose
To increase hardness and strength.
Process
Heating the metal to a high temperature and then rapidly cooling it in water, oil, or air. This process can induce stresses in the material.
03
Tempering
Purpose
To reduce brittleness after quenching and improve toughness.
Process
Heating the quenched metal to a lower temperature (below its critical point) and then cooling it, allows for some of the internal stresses to be relieved.
04
Normalizing
Purpose
To refine the grain structure and enhance mechanical properties.
Process
Heating the steel above its critical temperature and allowing it to cool in air. This results in a uniform microstructure.
05
Hardening
Purpose
To increase hardness and wear resistance.
Process
Involves quenching, followed by tempering to achieve desired hardness levels, commonly applied to tool steels.
06
Case Hardening
Purpose
To harden the surface of a material while maintaining a softer, ductile core.
Process
Methods include carburizing (adding carbon) or nitriding (adding nitrogen) to the surface layer, followed by quenching.
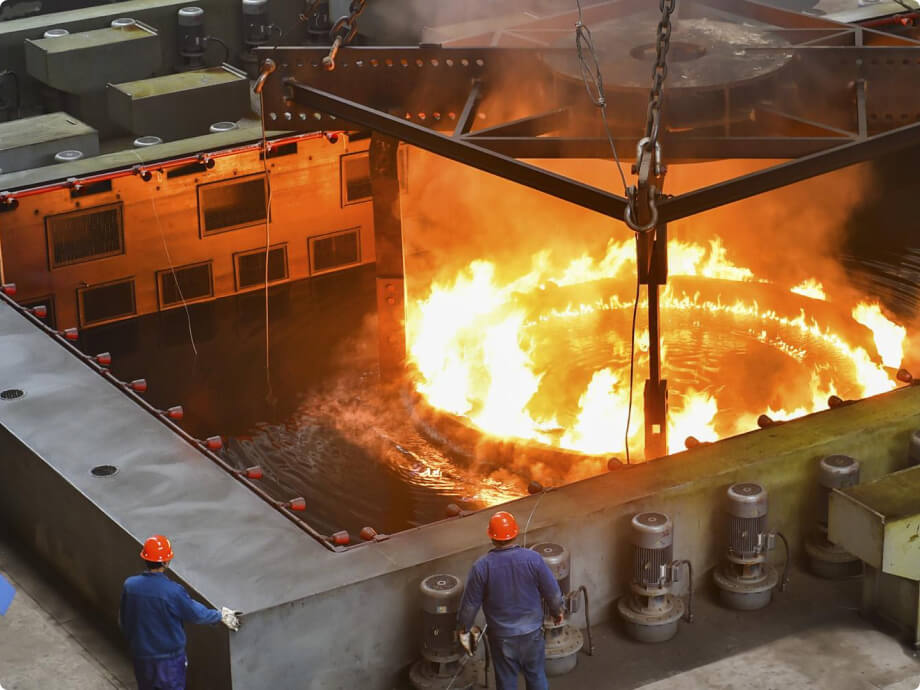
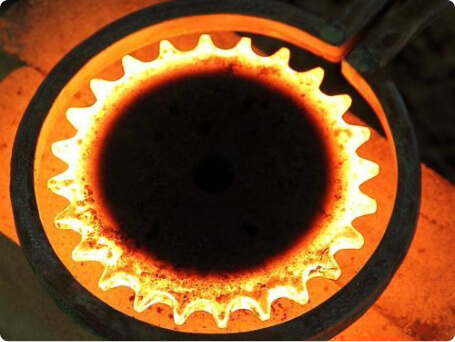
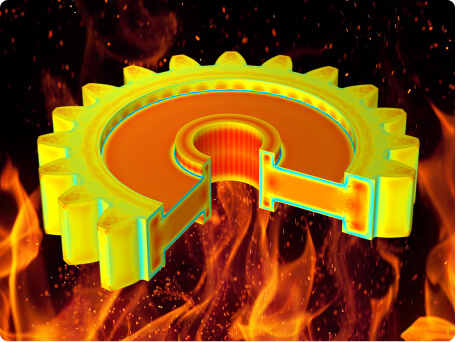
Manufacturing Capacity of Gear Shaft
Item | Description |
Gear Type | Worm Shaft & Worm Gear |
Module (m) | Max 30 |
DP | Custom-made |
Pressure angle (α) | 20 Deg |
Helix angle (β) | Max 35 Deg |
Number of teeth (z) | Custom-made |
Facewidth (b) | 800mm |
Profile shift coefficient (x) | Customized |
Face width (b) | Customized |
Length | Max 5 Meter |
Quality Control of Gear Shaft
Quality control is essential in the manufacturing of spur gears to ensure they meet specified standards and function effectively in their applications. The following are key aspects and methods used in the quality control process for spur gears: